Industrial gas leak detector play a vital role in ensuring early detection of leaks and prompt response to prevent accidents. This article provides comprehensive guidance on choosing and installing industrial gas leak detectors for optimal safety in industrial environments.
Understand the Types of Gas Leak Detector
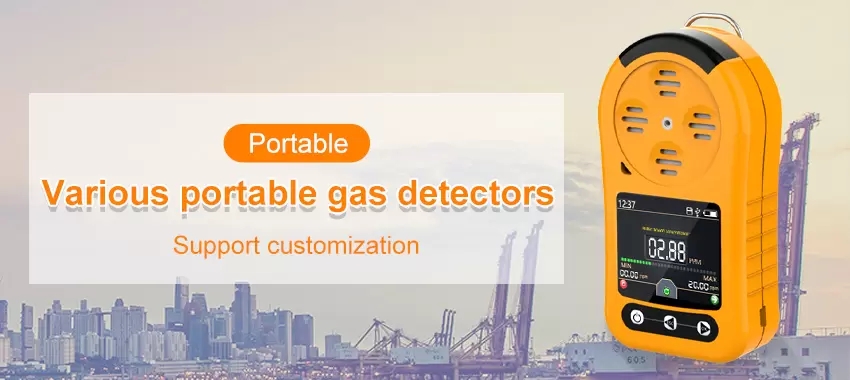
There are several types of gas leak detectors available, each designed for specific applications. Understanding these types will help in choosing the right detector for your industrial facility:
- Catalytic Bead Sensors: These detectors are suitable for detecting flammable gases. They work based on the principle of a heated catalyst that reacts with the gas, leading to a change in resistance and triggering an alarm.
- Infrared Sensors: Infrared gas detectors are effective for detecting hydrocarbon gases. They work by measuring the absorption of infrared radiation by the gas molecules.
- Photoionization Detectors (PID): PID detectors are ideal for detecting volatile organic compounds (VOCs). They operate by ionizing gas molecules when exposed to light, producing a measurable current that indicates the presence of gas.
- Ultrasonic Detectors: Ultrasonic gas leak detectors use ultrasonic sound waves to detect leaks. They are useful for detecting pressurized gas leaks in pipes and valves.
Consider Environmental Factors
Before selecting a gas leak detector, it is essential to assess the environmental conditions of your industrial facility. Factors to consider include temperature extremes, humidity levels, presence of dust or chemicals, and potential interference from other equipment. Choosing a detector that can withstand the environmental conditions ensures its long-term reliability and accuracy.
Evaluate Sensitivity and Detection Range
Different gas leak detectors have varying levels of sensitivity and detection range. It is important to choose a detector with the appropriate sensitivity to detect gas leaks at the desired threshold. Consider the potential sources of gas leaks in your facility and select a detector that can effectively detect gas concentrations within the required range.
Assess False Alarm Probability
False alarms can lead to complacency among the workforce and compromise safety. It is crucial to select a gas leak detector with a low false alarm probability. Look for detectors with advanced algorithms and self-diagnostic features that minimize false alarms caused by environmental factors or instrument malfunction.
Maintenance and Calibration Requirements
Regular maintenance and calibration are essential for the reliable functioning of gas leak detectors. Consider the ease of maintenance and calibration when choosing a detector. Look for detectors that have simple calibration processes, readily available calibration gases, and clear maintenance guidelines.

Proper Installation and Placement
Installing gas leak detectors correctly is crucial for their effectiveness. Consider the following guidelines:
- Position detectors at a lower level since gas tends to accumulate closer to the ground.
- Install detectors near potential leak sources, including valves, pipes, equipment, and storage areas.
- Ensure that detectors are easily accessible for maintenance and calibration but secure from vandalism or tampering.
- Follow the manufacturer’s instructions and industry guidelines for proper installation and wiring.
Conclusion
Investing in reliable industrial gas leak detectors is a critical aspect of ensuring safety in industrial environments. By understanding the different types of detectors, considering environmental factors, evaluating sensitivity and detection range, assessing false alarm probabilities, and following proper installation guidelines, industrial facilities can enhance their safety measures and mitigate the risks associated with gas leaks. Remember to regularly maintain and calibrate the detectors to ensure their ongoing accuracy and effectiveness.